Clean Energy Goals? Meet Modular Construction
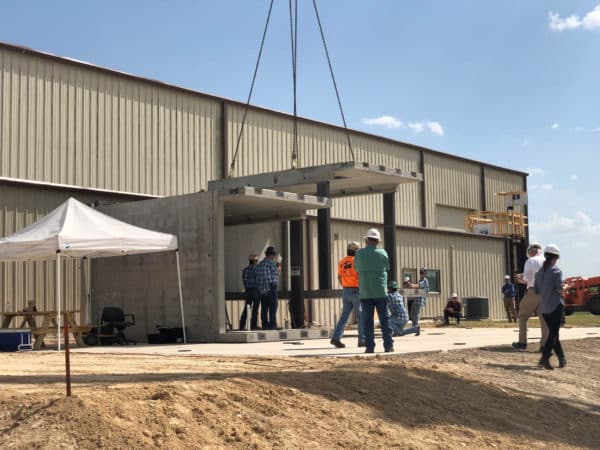
According to the World Health Organization, a rapid scale-up of available clean energy solutions must occur before 2030 to have a chance of meeting targets.
Available solutions need to achieve 8,000 GW of renewable energy, up from 2,800 GW currently; by 2025, 100 countries should establish targets for 100% renewable-based power. With this in mind, the share of fossil fuels in the global mix would need to fall from the current 60% to 30% by 2030. In financial terms, this means that an investment in clean energy must increase from the $500 billion in 2020 to $5 trillion per year by 2030. The United States has committed to cutting greenhouse gas emissions 50-52% below 2005 levels by 2030 requiring a large amount of new infrastructure investment!
As the demand for renewable energy ramps up, the financial investment for infrastructure and support projects is also increasing with the goal of bringing renewable infrastructure online as quickly as possible. This push towards new infrastructure requires a focus on process intensification (PI), a concept that dates back to the 1970s, that aims to dramatically improve manufacturing processes through the application of novel processes and equipment. PI pushes toward step changes in energy efficiency, capital cost reductions, and environmental impact. The construction industry applies PI using modular manufacturing for all kinds of projects including infrastructure design, process facility technology, and building projects.
As part of PI, modular construction establishes a manufacturing process intended to scale with the design from pilot stage to full scale, that allows for a stable supply chain and a controlled environment for manufacturing that increases quality and control. The biggest benefits of using modular manufacturing for processing facilities include lower project risks, compressed schedules, and reduced cost uncertainties – i.e., economy and efficiency.
Designing for Safe Operation
Designing with a focus on safety is critically important for renewable technologies having flammable, toxic, and/or explosion hazards. Modularized process design has the added advantage of allowing the project team to efficiently and cost effectively make safety central to the core design by having focused studies on hazard identification and operability (HAZID and HAZOP, for example) at the early stages of the design for each module. This allows the design team to address risks and lock in safety features before scale-up minimizing surprises during final design and/or construction. While the project team still needs to focus on site specific safety considerations and may need to conduct additional safety studies that include review of safety critical process controls, leak detection placement, fire protection, and emergency response, the initial focus on designing for safety enables efficiencies for each project that uses the given modular process design. Lastly prior to construction, a study to evaluate the siting of personnel in accordance with API RP 752 and API RP 753 is essential. Sometimes this may get lost in a compressed project schedule and then has to be addressed after construction is completed. Since many of these installations could be near the end users, often offsite, mitigating the risk after construction can be costly. A company such as BakerRisk working with the project team can assist with defining baseline hazard boundaries at the site selection phase and support the permitting process, with the possibility to update the study as design details become available.
Top 3 Considerations for Occupied Buildings
While renewable energy innovation and infrastructure is booming, existing experience with key low-carbon chemicals provides an understanding of the hazards and potential risks to personnel. Have you given thought to the following potential hazards with respect to your renewable project?
- Explosions. Hydrogen is a highly reactive fuel that may result in high blast loads in the event of an explosion.
- Toxics. Ammonia (which is quickly becoming an important hydrogen carrier) is a toxic material that may be lethal at high concentrations or in the event of prolonged exposure.
- Fires. Low carbon fuel feedstocks and products are often flammable and pose both fire and explosion hazards.
While there are a number of other risk concerns for occupied buildings associated with renewable energy operations, these three stand out as important risk drivers. However, consideration should also be given to other hazards such as extreme weather events (i.e., hurricane or tornado) as well as exposure to existing infrastructure. Recognizing nearby hazards, either within your existing facility or a neighboring industrial operation, are critical to understanding the new sustainable infrastructure risk exposure. With proper planning even the most aggressive project timescales can be met to ensure a safe and sustainable infrastructure is provided.
The Benefits of Modular Building Designs & Construction
Buildings are often the critical path for many project schedules – modular buildings provide a great solution for new design renewable infrastructure because of their schedule efficiencies, cost of construction, and quality control. Unlike traditional stick-built buildings, modular construction is typically self-supporting and can be placed directly on a prepared foundation. Modular buildings arrive on site in pre-fabricated components, which allows the key structural components of the structure to be manufactured in a quality controlled environment offsite where external impacts are minimal.
Efficient Schedule: Modular buildings have several important schedule advantages that traditional stick-built buildings do not.
The design and engineering phases of the project schedule are significantly minimized.
A building can be designed and engineered once to meet project requirements and be utilized at multiple locations without significant change.
Through robust supply chain and standardized design, lead times are minimized to the extent possible in a given market.
Offsite fabrication of key components limits schedule deviations and onsite disruption.
Minimal onsite time means lower risk to workers and personnel.
Cost Effective: There are three key cost advantages for modular buildings.A compressed project schedule saves on design, engineering, and construction labor costs through reduced man hours.
Offsite fabrication of key components means less onsite time is required for construction – saving on travel costs, per diems, and onsite labor rates.
Standardized key structural components saves on costs of customized design features.
High Quality: Modular building construction allows for greater product control.
Offsite manufacture of key components, especially those associated with the protection of personnel, allows skilled contractors to perform critical tasks that may otherwise need to be completed by subcontractors onsite.
Controlled environment prevents impacts from weather and other external hazards present at a construction site.
Components are inspected and tested to ensure high quality prior to arrival on-site. Any issues can be corrected in the fabrication locations rather than in the field on an as-needed basis.
While modular construction has many advantages and benefits, stick-built construction has continued to remain the go-to-solution for high-hazard locations where building function and comfort are important. Stick-built buildings can be designed for a site’s specific hazards, which may include blast, fragment, fire, and toxic exposures, while remaining a nice building to work in. However, the time required for a designed-for-purpose stick-built building may delay the schedule needs of the rapidly growing renewable energy infrastructure.
Traditional Stick-built Buildings vs. Permanent Modular Construction
Historically, there have been tradeoffs between purpose designed stick-built buildings vs. modular construction, including budget, timeline, and design requirements. As modular buildings have gained in popularity, many providers of modular buildings have chosen to sacrifice building specific design and functional requirements associated with stick-built buildings to gain the benefits of efficiency in design, engineering, and schedule associated with modular buildings. For this reason, many choose to go with stick-built buildings so that they can have customization and design flexibility for these expensive buildings.
However, a new market product provides the benefits of modular construction as well as the customization flexibility of stick-built buildings. FORTRESS Protective Buildings, LLC provides the benefits of modular construction in a permanent building that meets the life-safety design and functional characteristics of a stick-built building. Constructed of 8-inch reinforced precast concrete, FORTRESS’s modular buildings are designed and engineered such that over a 45-year facility design life, FORTRESS is approximately 1/3 the overall cost of a similar size modular steel building designed for temporary needs. A large portion of the cost savings of FORTRESS over a steel blast resistant modular (BRM) building is that unlike the steel BRM that needs to be replaced on average every 10 years, FORTRESS is a true permanent building comprised of modular components.
A New Building Product for Modular Construction
With 35 years of risk assessment and related industry expertise, Baker Engineering and Risk Consultants, Inc. (BakerRisk®) knows the hazards that renewable energy providers face. BakerRisk combined this expertise with their experience in designing protective buildings to create FORTRESS – a company that provides your staff a building proven to protect them while providing a functional and comfortable working environment. BakerRisk and FORTRESS understand that the design, engineering, and construction of your essential buildings must keep pace with your overall project schedule and safety of your employees and have designed a permanent building solution that easily adapts to your functional needs. This option requires only utility connections and a concrete pad to achieve low personnel risk exposure.
FORTRESS, unlike other industrial blast resistant buildings, has been subjected to a full-scale testing program to confirm occupants of the building are exposed to negligible vulnerability for design basis events. FORTRESS is designed and tested to:
FORTRESS Protective Buildings: Unparalleled proven protection for your site’s personnel – where sustainability meets safety.
Blast: 8 psi overpressure at >> 200 ms (long duration)
- Negligible occupant vulnerability
- Reusable and occupiable after safety checks/minor repairs following design basis load
Fragmentation: 13 lb projectile at 171 ft/s (116 mph) velocity
- Very minor local spalling observed
Thermal: 1-hour direct impingement for ¼-inch saturated propane jet fire
- Local spalling observed on the building exterior, but internal air temperature < 139 ºF and negligible smoke/toxic off-gassing
Toxic: < 0.1 ACH infiltration for main building and < 0.03 ACH infiltration for interior Shelter-In-Place (SIP) room (if selected)
- SIP Control Box, designed and engineered to provide system specification
- Extreme Weather: Resistant to high wind and debris from hurricane and tornado natural hazards
For every renewable hazard, there is a FORTRESS built from a modular design. Enhance your modular project design package with a FORTRESS to provide your team or your clients’ teams with maximum safety because a safer today means a more sustainable tomorrow.