Designing Beyond API RP 752/753 Compliance
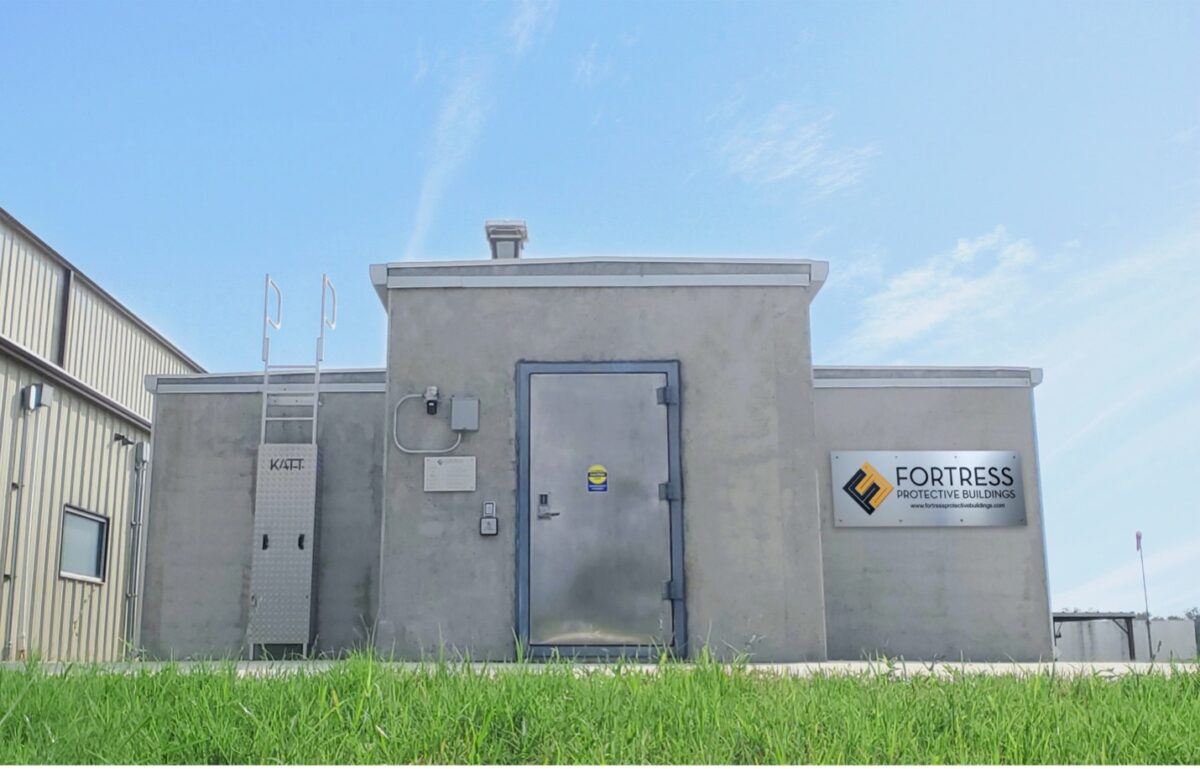
How FORTRESS blast resistant buildings offer ultimate protective capabilities
API Recommended Practice 752 and 753 are considered the go-to guidelines when siting protective structures designed and constructed for operational hazards. However, siting blast resistant buildings that only address blast hazards may not be maximally effective at protecting personnel against other industrial dangers, such as fire or toxic hazards, which also need to be accounted for to comply with API RP 752 and 753. When purchasing a building for compliance, it is important to ask the question — have all hazards been properly addressed in the building design?
FORTRESS blast resistant buildings (BRBs) are designed not only to protect against blast, fire, and toxic hazards as required by API RP 752/753 but also to provide protection from fragment and weather hazards. As a result, they offer an overall more effective structural solution for your facility’s personnel safety needs.
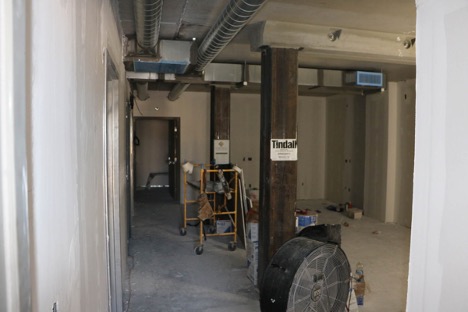
What are API RP 752/API RP 753?
API RP 752 and 753 are the “recommended practices” used to comply with OSHA’s facility siting requirements as part of the 1910.119 PSM standard. Both RPs were developed by the American Petroleum Institute, an organization established in 1919.
Comprised of several US oil companies, the API is now a national trade association that publishes many RPs to promote safety in the oil and natural gas industry. While the API has recommended practices for a variety of safety topics and needs, RP 752 and RP 753 exclusively focus on the safe placement of buildings.
Because the OSHA PSM standards are performance based and do not specify how to safely site occupied buildings (facility siting requirements), API RP 752 and 753 were developed to give facilities effective guidelines to follow when placing or constructing buildings in potentially hazardous areas.
API RP 752 – Management of Hazards Associated with Location of Process Plant Permanent Buildings
API RP 752 was first released in 1995 and has been updated twice to the current third edition published in 2009. It provides guidance for blast, fire, and toxic hazard evaluation and risk management when installing permanent buildings in facilities with hazardous operations. API RP 752 is the governing recommended practice when designing and placing permanent BRBs.
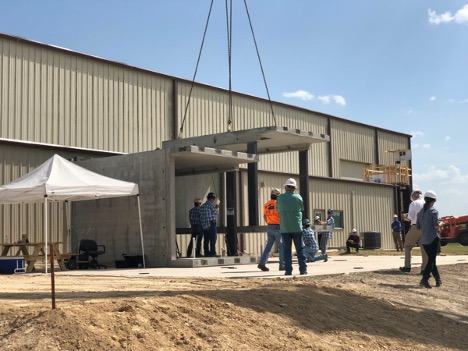
API RP 753 – Management of Hazards Associated with Location of Process Plant Portable Buildings
API RP 753 was initially published in 2007 as a response to the BP Texas City incident to address the fact that portable buildings, by their very nature, do not need to be placed close to hazardous processes. Unlike API RP 752, API RP 753 covers guidelines for hazard management for portable or temporary structures, including blast resistant buildings when used as temporary portable placements.
However, when portable modular buildings, including blast resistant modules (BRMs), are used to create a permanent building, API RP 752 is the applicable RP that should be used for safe placement (i.e., no longer a temporary installation).
API RP 752 and 753 revisions
API has a process for continuous improvement of all of their recommended practices that incorporates new learnings and address gaps in existing RPs. API has formed a committee to review and update both API RP 752 and 753.
One area for improvement is to make sure that fire and toxic hazards are addressed with the same robustness as vapor cloud explosion events. Vapor cloud explosion events are dangerous, but so are fire and toxic hazards. Facility siting studies should focus on all three hazards, and the building design and placement process should ensure that building occupants are protected from the process hazards that impact the location.
For example, a company installing permanent buildings with their focus only on blast hazards may design structures with a heavy bias toward materials or components that can resist blast loads and not properly account for a wider range of potential hazards such as:
- Fragment damage
- Thermal loads (i.e., industrial fires)
- Gas ingress (e.g., flammable and/or toxic material releases, natural gas leaks, etc.)
- Severe weather hazards
When a building is designed and constructed while only taking blast hazards into account, the building may not offer protection to occupants from other pertinent hazards and unintentionally place personnel at risk.
How FORTRESS blast resistant buildings are different
FORTRESS protective buildings are intentionally tested and designed to solve these potential vulnerabilities. Compared to other blast resistant buildings, a FORTRESS may offer enhanced defense against a wide range of possible worksite dangers, including explosions, fires, and toxic material releases.
At the same time, FORTRESS BRBs are constructed with full API RP 752/753 compliance. Each building is designed from modular, customizable building plans and constructed from precast reinforced concrete to offer excellent thermal and blast load protection. Reinforced concrete is a good choice for fixed protective structures that need to defend against hazards of any type.
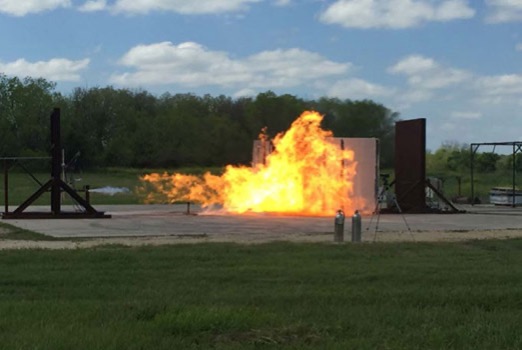
Designed and tested for key criteria
Many blast resistant buildings are designed by first identifying and specifying an upper design blast load, then performing dynamic analyses to ensure that the building’s structural components meet the required response limits.
This blast-load-focused design philosophy oftentimes ignores the secondary impacts that nonstructural components (e.g., lighting implements, furniture, etc.) may have on the building’s occupants. Even worse, the above philosophy doesn’t solve for additional possible hazards, such as fires, toxic gas, and more.
To counteract this, the design of FORTRESS blast resistant buildings was tested against several major threats to verify the following specifications:
- Blast loads — 8psi overpressure at >> 200ms (long-duration). This provides negligible vulnerability to occupants plus ASCE Low Response.
- Fragmentation danger — 13 lb. projectiles launched at 171 ft./s (160 mph) velocities. Non-hazardous local spalling is observed during these tests.
- Thermal loads — 1-hour direct impingement for ¼ inch saturated propane job fire. Non-hazardous local spalling is observed on test building structures, but internal air temperature remains at <110°F with negligible smoke/toxic off-gas.
- Toxic hazards — <0.1 ACH infiltration for main buildings and <0.03 ACH infiltration for interior Shelter-In-Place (SIP) rooms. These tests utilize an SIP Control Box designed for life safety.
- Extreme weather hazards — Resistant to high winds as well as debris from hurricanes and tornadoes.
FORTRESS protective buildings provide not only the protection required by API RP 752 and 753 for blast, fire, and toxic events but also provide fragment and severe weather protection. Contact us today for more information.